How To Help Businesses
The information system can handle a large amount of related information, including equipment malfunction or failure, so that companies can fully understand the maintenance cost, the history of equipment operation, etc., as these information about safety, cost, production capacity, quality, etc., are all influential factors on the business operation, which will help to optimize the on-site operation and maintenance and serve as reference for quick response to the decision-makers.
Hon-Tsai technology-guided inspection management system uses RFID and handheld mobile devices (such as tablet and smartphone) to assist companies in managing the inspection. The supervisor can set up the schedule and inspection tasks in advance to minimize the impact of personnel’s experience. Combined with the RFID technology, the system ensures that inspections are managed in place. Patrol inspector will now only carry a handheld mobile device and avoid the inconvenience of carrying bunch of forms that all data can be uploaded directly to the back-end terminal of management system to be integrated in the database for big data analysis.
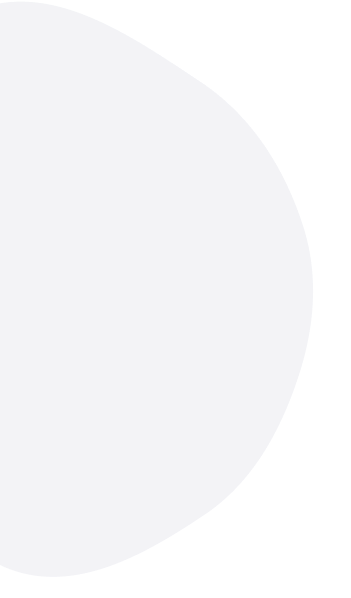
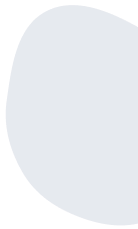
Design Concept
Inspection with expert evaluation
The objective is to establish a standardized (with SOP) and experiential information system to provide specific criteria of inspection for determining problems on site.
Inspection with digital dashboard
The system will convert the collected data from daily inspection into useful knowledge for operator to make decision and manage some of unquantifiable or non-qualitative tasks.
Inspection with equipment maintenance record
The system provides basic information and status quo of equipment in operation, which shall significantly reduce the impact of inexperience during personnel changes.
Inspection with 5G network and AIoT
The system uses the advanced information technology (AIoT) to assist in autonomous inspection and management of equipment, including real-time data transmission and monitoring to save cost and improve the efficiency and accuracy of decision-making.
Inspection with chart dashboard
The system will conform with the requirements of PDCA management cycle and immediate reporting; for example, early detection/immediate response/avoidance of escalation of the situation!
Inspection with BI
The system will build large database upon the equipment operation data from inspections to help companies to conduct business within the requirements of clean and safe operation by using systematic technology and control measures.
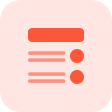
System Overview
- Standard
- Optional
Front-end inspection module
- Android 10 on mobile phones/tablets
- Windows 10 or above (tablet, RFID/NFC, QR Code)
- Support for Traditional Chinese
- In-position verification
- Routine inspection
- Snapshot
- Notification of imminent expiration or not-in-position (via E-mail or APP)
- Support iOS 14 phones/tablets
- Support wearable devices
- Support one-dimensional barcode or GPS
- Support English, Vietnamese
- APP for supervisory inspection work
- Wireless transmission of test instrument
- Dispatchment of personnel for improvement operation
- Notification of imminent expiration or not-in-position (via LINE or SMS)
Report and statistics module
- Daily record of in-position verification
- Monthly report of daily point inspection
- Inspection performance statistics
- Preventive maintenance record
- Daily automatic inspection checklist
- Monthly automatic inspection checklist
- Field operation record form
- Instrument audit log
- Chemical audit log
- 5S checklist
- Rotating machinery operation log
- Temperature measuring inspection log
- Situational digital dashboard
Record query module
- Front-end response record query
- Web query of exception record
- Snapshot query
- Inspection statistics query
- Inspection/Time query
- Front-end non-response record query
- Exception query via APP
- Specific event record query via APP
- Notification of not-in-position
- Supervisory audit query via APP
- Improvement progress query
- Monthly personnel-in-position statistics
- Monthly inspection item normal rate
- Monthly exception statistics
- Monthly sign-off statistics
- Inspection item run charts
- Cumulative inspection item run charts
- APP with statistical charts on inspection records
- APP with equipment query run charts
System management module
- Account access privilege management
- Inspection route management
- Inspection range setting
- Inspection point management
- Inspection route planning
- Inspection area management
- Equipment and inspection item management
- Form module management
- Inspection time setting
- Records audit management
- Improvement operation
- Web input mode
- Mobile device management
- Scheduling and attendance
The system on PC has a web-based interface for control and browsing and has no limit on the number of users. The front-end mobile device(such as smartphone or tablet) also supports Windows, iOS and Android operating systems.
Various in-position verification methods(including ID check/QR code/RFID/NFC/GPS) are provided according to the on-site environment.
The checklist is now fully electronic (paperless), which covers full parameter settings to allow autonomous maintenance of the system.
The personnel-in-position checklist, manual meter reading record,supervisor sign-off sheet, exception tracking,etc., for which all of the inspection tasks are now informatized.
The system allows an immediate report and tracking mechanism for quick response to any exceptions on site.
It is imperative to pinpoint the exact location of all inspection points, which can be reported in combination with electronic maps and cadastral information.
- The use of smart device to sense RFID or NFC allows real-time inspection, recording and supervisory audit.
- Smart device can be used for real-time inspection,data display and printout report.
The system provides expandable equipment warranty and inspection operations to build the maintenance record of critical equipment, which can also be integrated with CMMS.
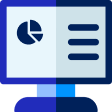
Product Description
- It can be used on a variety of front-ends, such as smart phones, tablet computers, etc., that the inspector is used to, in order to shorten the time to adapt to the system.
- The system supports mobile devices with Android 10, iOS 14 and Windows 10 operating systems.
- The interface is in Traditional Chinese, Simplified Chinese, English, and Vietnamese.
- Customers do not need to develop a separate front-end program and it provides a variety of recording for routine inspection, equipment malfunction, error item, and deactivation history, as well as different inspection modes with either activated or deactivated equipment, to satisfy various inspection requirements.
- The system provides six interface modes for different field environment and system expansion.
- Photographs for record is more direct and clearer than written or spoken words, as they will help the maintenance personnel to quickly determine the cause, shorten the repair time and reduce the chance of misjudgment of equipment malfunction.
- The imaging function also includes the ability to edit, store and delete photos. By photographing the exception event, it significantly reduces the time to organize and prepare relevant information for comparison and report.
- The interface is web-based, which is common for daily computing by the operator and also eliminates the need to install the system on multiple computers to synchronize the latest information.
- The system has server authorization check but does not limit the number of front-end and back-end users or set a time limit.
- The system supports a variety of in-position verification methods, including RFID/NFC (Note: Apple’s mobile phone only supports NFC), GPS positioning, and 1D/2D barcode, which can be applied to different operational environments, such as for security patrol, mechanical instrument inspection, power calibration, equipment maintenance record, fixed asset inventory, etc.
- It provides convenience for the personnel to select different mobile devices, data access mechanisms or recording methods for inspection in different environments.
- The system authorization has no limit on the number of positioning points and all of the above methods, such as RFID, QR Code and GPS, can all be used in combination.
- After completing the inspection work by using the smart guided system, the personnel no longer have the burden to manually jot down information on papers, because the system provides multiple functions (ex. In-position check-in, meter reading, photographing, video recording and handwritten remarks) to create and upload data (via 4G or Wi-Fi network) to the database and conclude the operation on site without the subsequent paperwork.
- The fill in and reporting of information on the inspection are completed in the process of informatization, which not only save time but allow the personnel to perform more troubleshooting, research and maintenance of equipment. Plus, the supervisor and other related departments can also inform the corresponding maintenance unit or outsourced manufacturer to prepare manpower and materials to improve work efficiency.
- The system supports equipment inspection (according to the inspection route), personnel inspection (according to the inspection area), and unspecified route (audited by the supervisor).
- The system also supports the sharing of front-end inspection equipment that one can be shared among personnel; for example, ten inspection assignments by routes can be completed by 3 personnel in a 24-hour shift.
- It has a user-friendly interface, which is easy to use and understand. The front-end interface displays assignments by color to distinguish the inspection task of the day or allow planning works ahead.
- Different job schedules can be customized according to different types of inspection, in which the system runs by the principle of automatic dispatchment based on the cycle of operation (such as by hour, day, week, month, half year, one year, or specific date); thus, reducing the time required of the supervisor to plan and schedule the inspection assignments.
- The digitalization of inspection management in the form of a standard electronic system will allow convenient and quick data retrieval, incident tracking and other related operations.
- Through the system, the latest relevant uploaded data can be directly inquired and accessed without waiting or urging the inspection personnel to perform statistical analysis on the data and track the exceptions, or spending time on organizing reports, all of which can improve the overall work efficiency.
- The system's notification module will report any event of personnel not-in-position and equipment malfunction. Once received by the supervisor, the most appropriate personnel can then be dispatched to deal with the situation, and it improves the response time of maintenance.
- It also shortens the time to determine on site or the time to report the exception.
- Inspection location and route can be planned ahead with electronic map.
- Through the map information, you can understand the public dangerous goods in the factory area, determine the type, quantity, classification and check whether the dangerous goods exceed the controlled quantity, as well as the floor plan and rescue information.
- The module can be integrated with the company’s own CMMS or PMS, for the inspection personnel to combine preventive maintenance or work order operations in one spot.
- When the supervisor signs off the operation, an online work order can be established for any exception handling of operating equipment in inspection.
- The supervisory audit functions include: snapshot, automatic retrieval of inspection record based on GPS positioning (requiring network connection), exception handling (the work order), cumulative inspection data charts, and equipment run charts.
- Supervisors can carry out auditing operations from time to time as unrestricted inspection tasks in the system, and any exceptions can be recorded in the form of notes and photos to be sent back to the back-end for dispatching designated personnel to carry out repair and maintenance.
- Customized procedure and report form are provided with adjustable parameters, which can greatly reduce the hours spent by personnel to organize inspection data, records, and report submission every month.
- It can shorten the personnel’s time spent on organizing the inspection data, records and reports for submission.
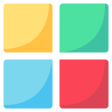
Application Level
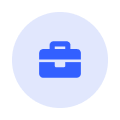
Automatic inspection (in accordance with the occupational safety and health management measures to implement pre-operation inspection, routine inspection and key inspection).
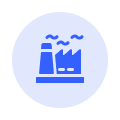
Petrochemical industry (long-distance pipeline oil transportation operation, natural gas transportation operation, oil tanker filling operation, oil tank inspection, work site equipment inspection, hazardous work and construction inspection at the plant site, etc.)
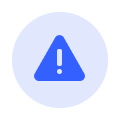
The location, structure, and equipment installation standards of manufacturing, storage, or processing sites for public dangerous goods and flammable high-pressure gases, as well as storage, processing, and transportation industries.
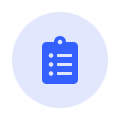
Inspection record (provides information on shift rotation, in-position checkpoint, security patrol and supervision, water and electricity meter reading, pipeline inspection, security guard posting at construction site, 5S principle, etc.)
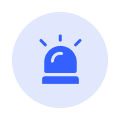
Business operator who needs immediate notification to quickly respond to handle the exception.
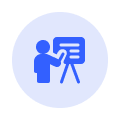
Business operator with rigorous requirement of tedious and extensive education and training process for newcomers.
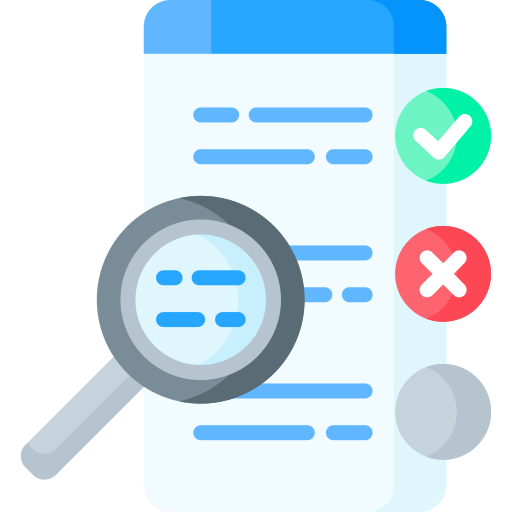
Inspection Smart work:Immediate detection of hazards provides quick payback.
Director sure audit:100% sign-off rate of inspection records.
Abnormal notify immediately:100% completion rate of hidden danger improvement.
Promote Equipment reliability:Really grasp the equipment maintenance time.
Equipment Health resume:Real-time and proactivecontrol of facility statues.
Inspection Maintenance record sheet:Comprehensive paperless reduction of secondary documents.
Establish Inspection SOP:Provide inspection experience inheritance tools.
Combat Service Digital Dashboard:Provide instant statistical analysis after inspection.
Precise Himan mastery:100% implementation rate every month.
Implement equipment service:Key set 100% set anchor point.
No warning malfunction repair:The number of major accidents per year can be set.
Combine IoT and graphics:Provide convenient record query tool.