How To Help Businesses
It is essential to conduct pre-operation inspections to prevent unexpected incidents.
In this era of digital technology management, Hon-Tsai Technology Co. plans to embrace digital transformation, allowing businesses to effectively implement automatic safety and health inspections and integrate them into management processes to replace the existing management methods. Mobile-enabled automatic inspection operations make inspections simpler and more convenient. A mobile-enabled automatic inspection management platform effectively controls the smooth flow of processes. It ensures compliance with the Occupational Safety and Health Act for pre-operation, regular, and focused inspections. Digitizing automatic inspections will enhance the efficiency of self-inspection and deficiency management. When deficiencies are identified during automatic inspections, the system immediately sends deficiency improvement notifications to the relevant responsible personnel, facilitating the process of addressing and improving deficiencies.
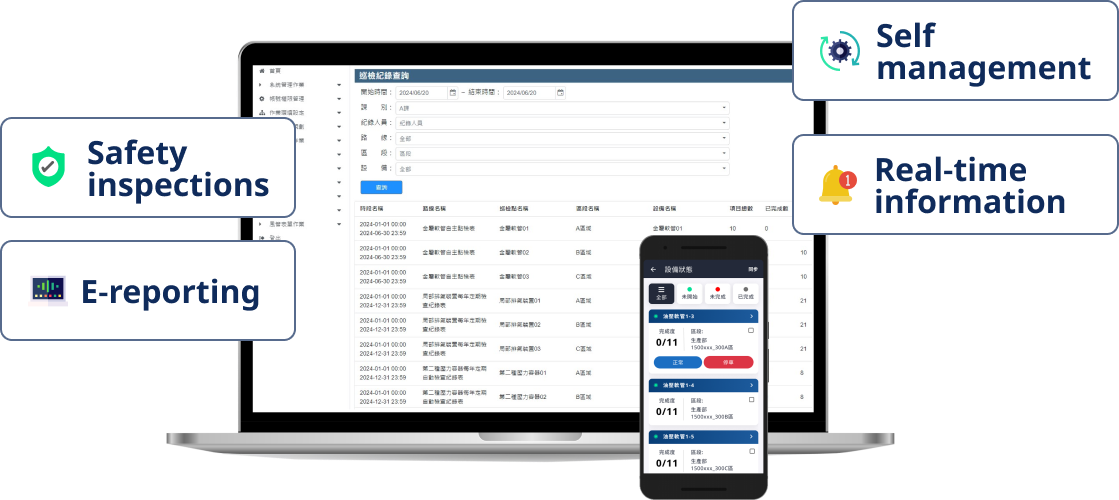
Legal basis |
---|
According to the "Occupational Safety and Health Act," Chapter 4, an automatic inspection plan should be established concerning automatic inspections conducted by employers as stipulated in Articles 13 to 63. Employers conducting regular inspections and focused inspections per Articles 13 to 49 should record the following information and keep it for three years: inspection date, inspection method, inspection area, inspection results, the name of the person conducting the inspection, and the details of the improvement measures to be taken based on the inspection results. Regarding handling abnormal inspection results, when workers, supervisors, and occupational safety and health management personnel conduct inspections and find abnormalities in the workplace, facilities, or personnel operations or potential hazards, they should immediately report to higher-level supervisors.This product assists businesses in establishing an automatic inspection management platform and supports more than 27 sample forms within the platform. To implement inspection tasks, a plan is made to provide inspection personnel with mobile devices and an app to execute automatic inspection processes. The system platform can incorporate the inspection plan content required by the company, including inspection equipment, inspection items, judgment criteria, inspection results, and more.Article 13: Regular Inspection Form for Motorcycles and Internal Combustion Engine Vehicles (Monthly) Article 14: Quarterly Automatic Inspection Form for General Vehicles Article 15: Regular Inspection Form for Vehicle Height Lifters |
Transformation
Feature
- Easy Operation: Automatic inspections are simplified and made more convenient through digital online reporting.
- Precise Control of Inspection Items: Digital automation ensures smooth process management and complies with the Occupational Safety and Health Act for pre-inspections, regular inspections, and critical inspections.
- Real-time Notifications and Reduced Occupational Hazards: When automatic inspections identify deficiencies, the system immediately sends improvement notifications to relevant personnel, reducing the likelihood of occupational accidents.
- Reduced Equipment Loss and Improved Management Efficiency: Digital inspection forms make it easy to collect equipment data. Recording data in the system allows for direct examination of causal relationships between equipment operations, helping identify and eliminate problems. This minimizes equipment losses and enhances management efficiency.
Resolve paper-based form filling
Electronic product input
System management reports
Advantage
- Eliminates the need for personnel to fill out manually and record inspections on paper, saving time and reducing errors.
- Improves data integrity by allowing direct electronic input, reducing the risk of tampering.
- Generates management reports through information systems, reducing errors associated with manual and paper-based operations and enhancing report reliability.
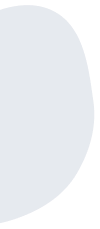
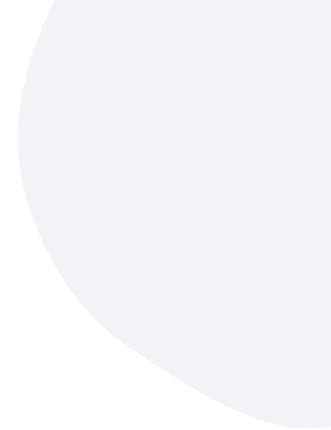
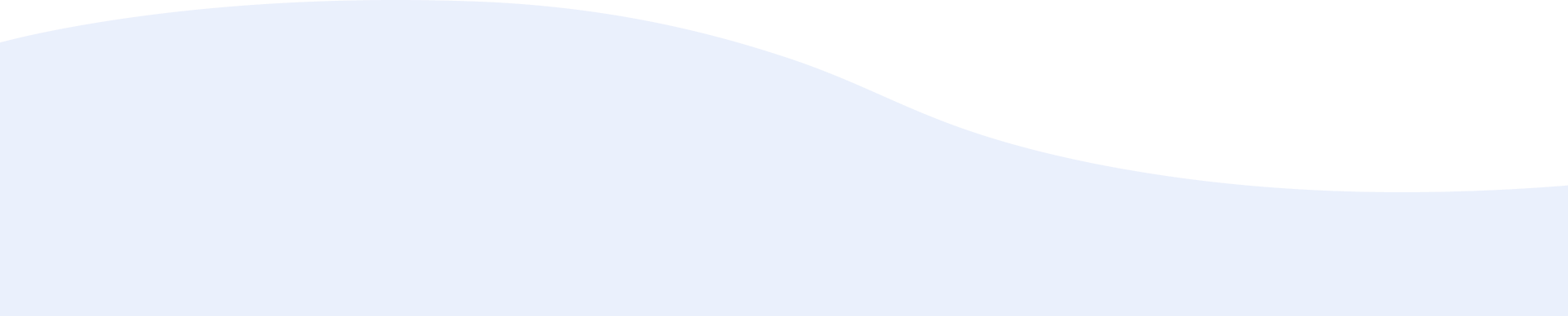
Solution
Inspection ESO
Front end mobile device module (Android, iOS), back end management module, and query operations.
Automatic inspection templates
Provides 27 standard automatic inspection templates (regular inspections, critical inspections, operational inspections) for factories or construction sites, following the Occupational Safety and Health Act.
Automatic inspection form(Excel)
Offers one automatic inspection form and Excel export of inspection results.
Hardware requirements
Hardware requirements include a server or cloud space (subscription-based), handheld mobile devices (Android or iOS), and RFID/NFC tags or QR codes.
Add-on items
Customizable reports and autonomous inspection forms can be added as options for individual construction project quality.
Application
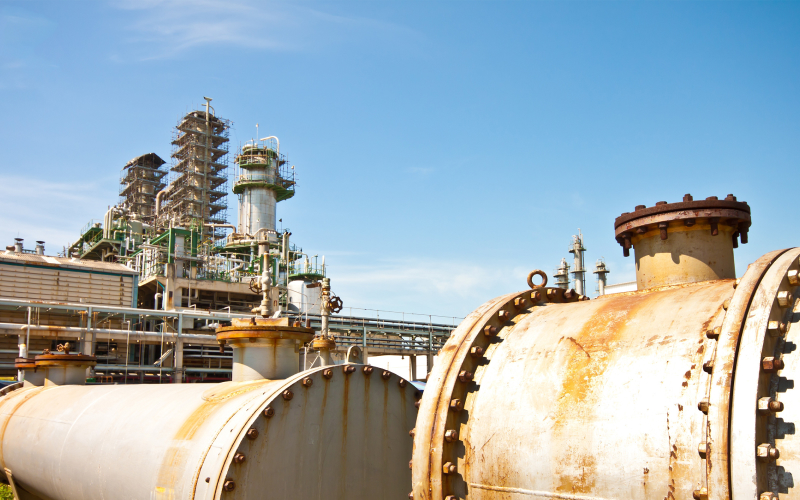
Petrochemicals
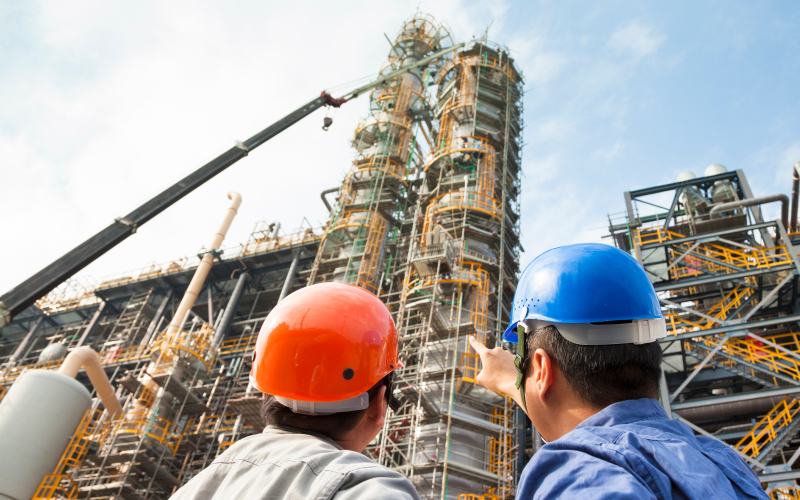
Construction
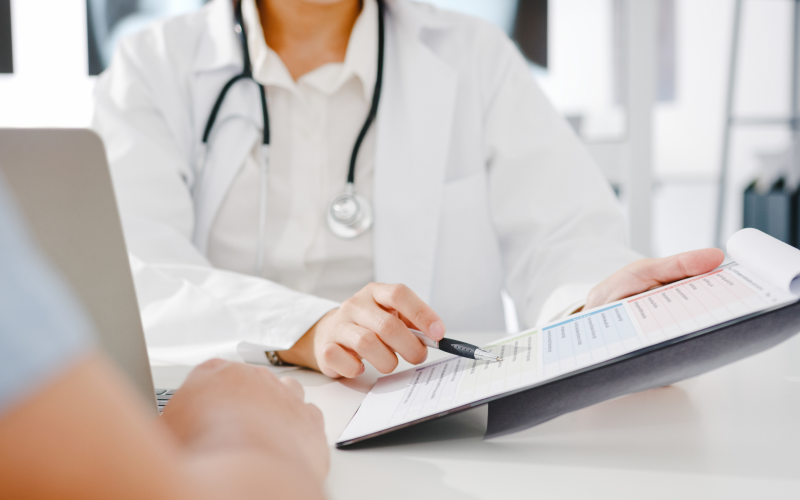
Hospital
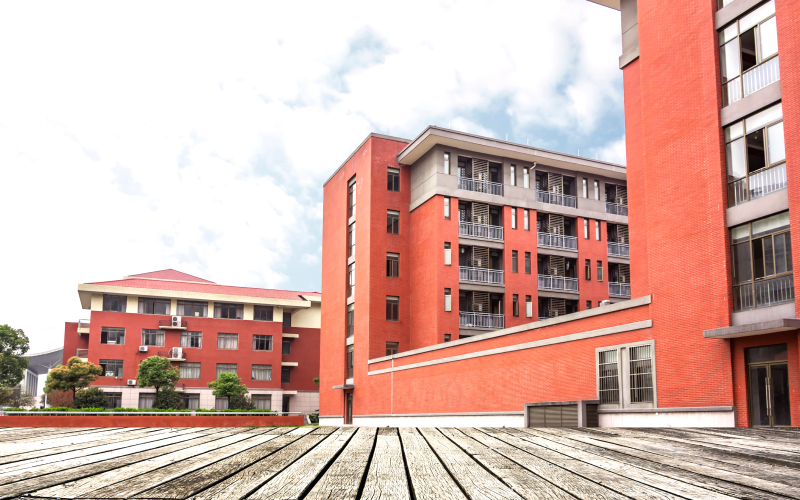
School
Relevant companies or units that comply with the Occupational Safety and Health Act, including industries such as petrochemicals, construction, healthcare institutions, and schools from high school level and above.