How To Help Businesses
Proactive Maintenance Scheduling
Considering the high vulnerability of critical infrastructure, businesses need to engage in self-reflection and examination. The interruption of essential facilities due to natural disasters or deliberate acts can significantly impact a company's everyday operations, the safety of personnel, property losses, social reputation, and even national security.
To ensure the continuity and resilience of a business, the primary focus should be safety and protection. Therefore, inspecting, checking, maintaining, and managing equipment is to proactively prevent issues, enabling swift responses and minimizing disaster-related losses.
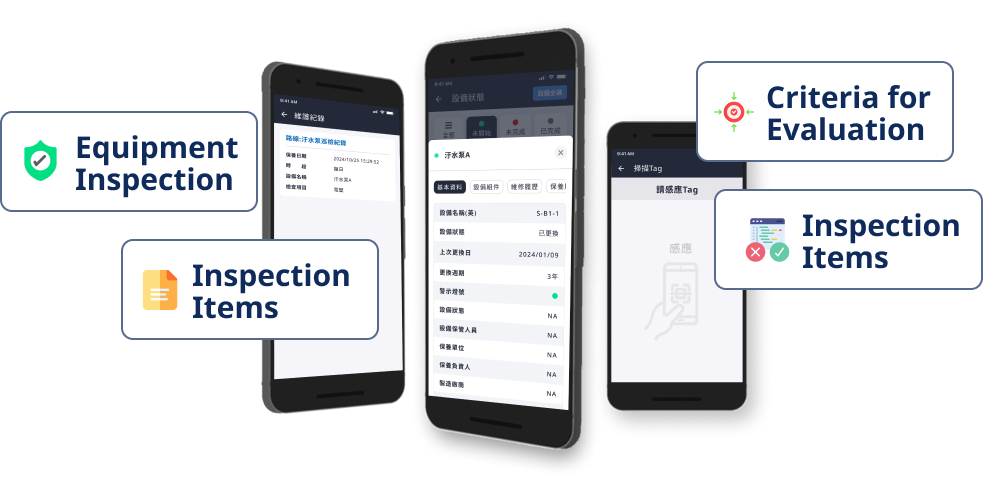
Problems | ||
---|---|---|
Traditional Operations: Various equipment inspection forms(Generator Daily Maintenance Record/Elevator Maintenance Checklis/Sewage Pump Inspection Record/Chiller Machine Log/Boiler Inspection Record) with inspection criteria based on the equipment specifications provided by the client. How do you handle it?Is data retrieval challenging? | ||
![]() Is it filled out on paper? |
![]() Scanned and archived? |
![]() Entered directly into electronic forms? |
Transformation
Feature
- Easy Operation: Equipment inspections in the factory premises are simplified and convenient through a digital handheld front end app-based checklist system.
- Precise Inspection Item Management: Digitalization of equipment inspections ensures smooth process control and compliance with occupational safety and health act, including regular and critical inspections.
- Real-time Reporting, Reduced Workplace Accidents: When equipment inspections identify deficiencies, the system promptly sends notifications for improvement to the responsible personnel, reducing the likelihood of workplace accidents.
- Minimize Equipment Loss and Enhance Management Efficiency: Digital mobile inspection forms make it easy to collect equipment data. Recording data in the system allows for the direct examination of cause-and-effect relationships between equipment operations, enabling timely identification, root cause analysis, and the elimination of defects, thus minimizing equipment loss, and improving management efficiency.
Establish a system for factory inspections
Understand the status of factory equipment
Solve the problem of personnel inspection
Electronic device input
System generates management reports
Establish equipment maintenance history
Combined with digital dashboard
Advantage
- Implement factory inspection procedures within the system framework to meet safety inspection standards.
- Audit or record abnormalities in the factory environment, keep track of potential factory environment hazards beyond equipment-related issues.
- Solve the inconvenience of manual paper-based inspections, where each item must be filled out, checked, and recorded individually.
- Improve the issue of easily tampered records by enabling direct data input through handheld electronic devices.
- Generate management reports via the information system to reduce errors caused by paper-based and manual processes, enhancing report reliability.
- Create equipment maintenance histories and access comprehensive equipment information and maintenance records.
- Combine information into digital dashboards to consolidate and optimize digital transformation efforts.
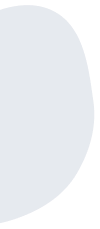
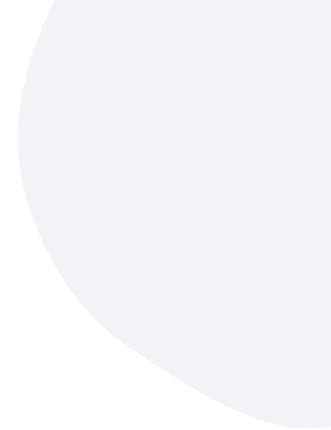
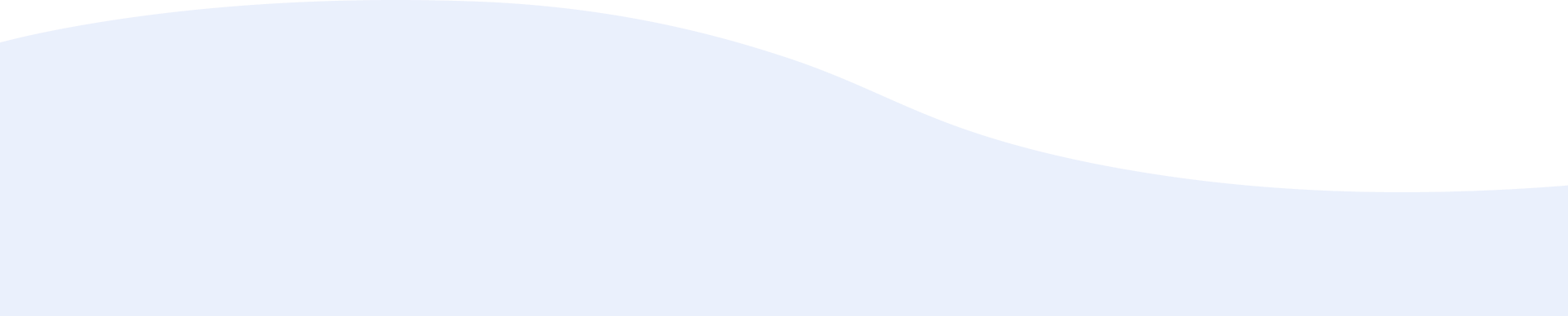
Solution
Guided Inspection Management System
Front end mobile device module (supporting Windows, Android, and iOS, available separately), back end maintenance management module, equipment history module, query and statistics module, electronic signature support.
Provide templates
Templates for Air Conditioning Units, Air Handling Units, Water Pumps, Generators, Elevators, and Boilers.
Provide reports
Three reports (Daily Inspection Records, Monthly Reports on Daily Inspection Records, Automatic Inspection-Daily/Weekly/Monthly/Yearly), a Scheduled Maintenance Calendar, and one digital dashboard.
Hardware Requirements
Server, Personal Computer, Tablet (Windows or Android), RFID/NFC Tags or QR Codes.
Add-on items
Customized report modules, scheduling modules, maintenance request modules, IoT (temperature or vibration sensing).
Application
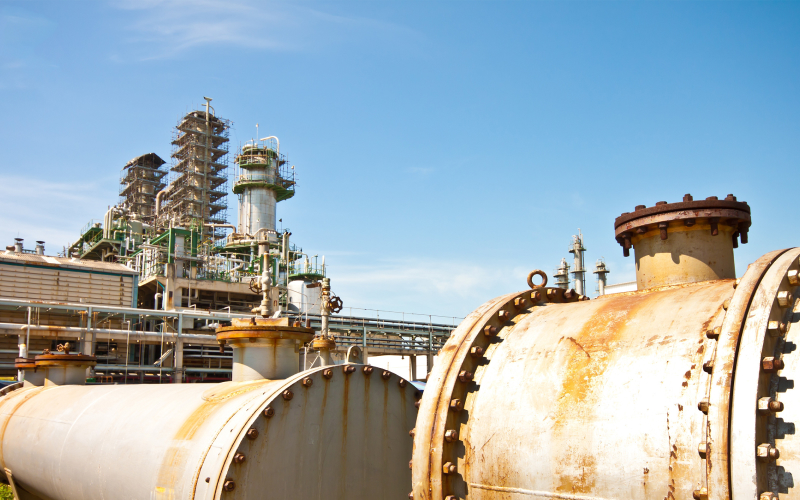
Petrochemicals
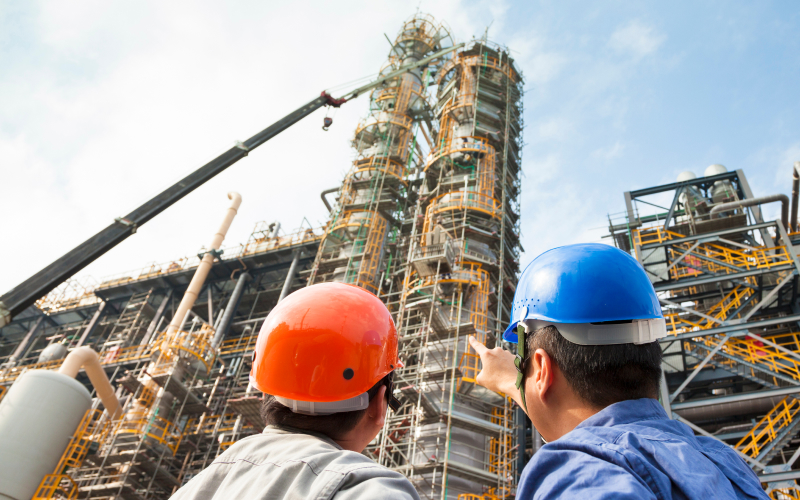
Construction
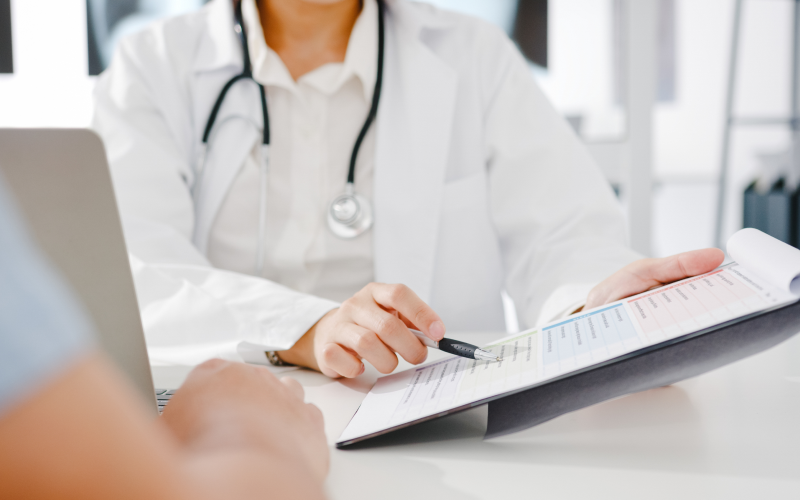
Hospital
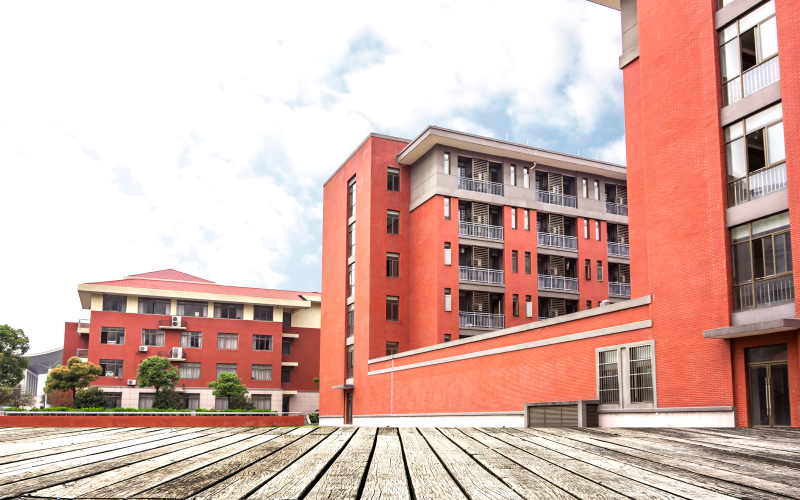
School
Relevant companies or units that comply with the Occupational Safety and Health Act, including industries such as petrochemicals, construction, healthcare institutions, and schools from high school level and above.